How to Ensure Quality Assurance in Pharmaceutical Supply Chains
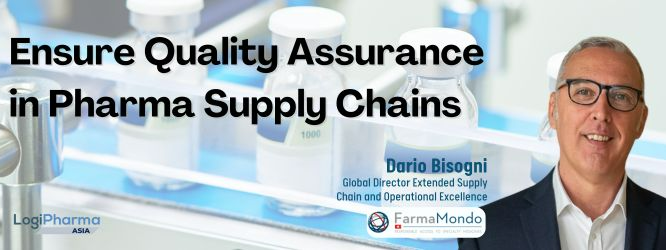
Global disruptions have put the pharmaceutical supply chain at risk of suffocating profit margins, skyhigh investments in temperature-controlled products, as well as strict regulatory guidelines.
What can firms do to counteract against these impending forces in the growing yet uncertain healthcare market? As the Head of Extended Supply Chain and Operational Excellence at FarmaMondo SA, Dario Bisogni shares his intriguing insights on how to maintain stringent Quality Assurance (QA) standards whilst facing unforeseen challenges. By leveraging on state-of-the-art technologies such as AI and blockchain, and strategic measures, he is able to enhance end-to-end visibility and trace every product at respective stages of its lifecycle.
By investing in temperature-controlled logistics, this ensures adherence to Good Distribution practice (GDP) standards without compromising on efficiency. He further emphasises on innovative training methods to keep staff updated on the best practices.
From diversifying its suppliers to partnering with logistics providers for efficiency in transporting their products, these are springboards in future-proofing your next strategy! He stresses the importance of maintaining operational flexibility in a strict regulatory environment, underscoring how superior QA can be a significant competitive advantage.
As the Head of Extended Supply Chain and Operational Excellence at FarmaMondo SA, how do you future-proof your supply chains to maintain QA standards while adapting to unforeseen challenges?
Future-proofing supply chains to maintain quality assurance standards in the face of unforeseen challenges involves a combination of strategic planning, risk management, technology integration, and agility. Here are some key strategies:
- Diversification of Suppliers, Risk Assessment and Management, Technology Integration, Collaboration and Partnerships, Flexibility and Adaptability, Continuous Improvement, Regulatory Compliance, Scenario Planning. To be more concrete: Diversifying your supplier base geographically and strategically can help mitigate risks associated with disruptions in one region.
- Tech. Integrations :Embrace digital technologies such as IoT sensors, blockchain, and AI to enhance visibility and traceability across the supply chain. These technologies can provide real-time data insights, enabling proactive decision-making and rapid response to disruptions.
By implementing these strategies, organizations can enhance the resilience and agility of their supply chains, maintaining quality assurance standards even in the face of unforeseen challenges.
What specific strategies can pharmaceutical companies implement to ensure adherence to GDP standards without sacrificing efficiency in their logistics and distribution processes?
Ensuring adherence to Good Distribution Practice (GDP) standards is crucial for pharmaceutical companies to maintain the integrity and safety of their products throughout the supply chain.
Let me share what are specific strategies they can implement to achieve this without sacrificing efficiency in logistics and distribution processes: Invest in Temperature-Controlled Logistics, Implement Real-Time Monitoring, Optimize Packaging Design, Streamline Supply Chain Processes, Ensure Compliance Training, Enhance Visibility and Traceability, Collaborate with Logistics Partners, Implement Contingency Planning, Monitor and Measure Performance.
- Invest in Temperature-Controlled Logistics: Many pharmaceutical products, especially biologics and vaccines, are sensitive to temperature fluctuations. Investing in temperature-controlled packaging, storage facilities, and transportation systems helps maintain product integrity during transit.
- Streamline Supply Chain Processes: Identify and eliminate inefficiencies in supply chain processes, such as redundant paperwork, manual data entry, and unnecessary delays. Implement digital solutions (e.g., electronic data interchange, blockchain) to automate and streamline documentation and communication.
By implementing these strategies, pharmaceutical companies can maintain adherence to GDP standards while optimizing efficiency in their logistics and distribution processes, ultimately ensuring the safe and reliable supply of pharmaceutical products to patients.
How is FarmaMondo SA leveraging technology (e.g., real-time temperature monitoring, blockchain, IoT) to streamline QA processes while maintaining GDP compliance?
FM as other Pharmaceutical Companies are leveraging various technologies to streamline quality assurance (QA) processes while maintaining compliance with Good Distribution Practice (GDP) standards.
Here's how they are using technology: Real-Time Temperature Monitoring Sensors and Trackers, Data Analytics and Predictive Modeling, Supplier Relationship Management (SRM) Platforms.
As for Data Analytics and Predictive Modelling: Advanced data analytics techniques, including machine learning and predictive modelling, are used to analyze large volumes of supply chain data and identify patterns, trends, and potential risks. By leveraging historical data and predictive algorithms, pharma companies can forecast demand, optimize inventory management, and anticipate potential quality issues before they occur.
When integrating these technologies into their QA processes, FM and pharmaceutical companies can enhance efficiency, transparency, and compliance while ensuring the safety and efficacy of their products throughout the supply chain.
What are innovative training methods to ensure staff stays current on best practices without sacrificing operational efficiency?
Innovative training methods can help ensure that staff stays current on best practices without sacrificing operational efficiency.
Here are some examples that I know: Mobile Learning Apps, Virtual Reality (VR) Simulations, Metaverse learning, Peer Learning Communities, Personalized Learning Paths.
As a Company, we have launched an AI project to adopt new technologies and grow in market competition. This can ensure that staff stays current on best practices while maintaining operational efficiency.
Can you share examples of successful partnerships or collaborations that FarmaMondo SA has engaged in implementing best practice QA protocols throughout the pharmaceutical supply chain, especially in the context of global distribution networks?
FM and Pharmaceutical companies frequently engage in partnerships and collaborations to implement best practice QA protocols throughout their global distribution networks. Here are some examples: Partnerships with Logistics Providers, Collaborations with Technology Providers, Industry Partnerships and Consortia...
Partnerships with Logistics Providers: Pharma companies often partner with specialized logistics providers who have expertise in pharmaceutical transportation and distribution. These partnerships involve close collaboration to ensure adherence to GDP standards, including temperature-controlled transportation, real-time monitoring, and secure handling of pharmaceutical products. For example, companies like DHL, FedEx, and UPS have established dedicated healthcare logistics divisions to support the unique requirements of the pharmaceutical industry. As a Company we are working with this Partners on that.
These examples demonstrate the importance of partnerships and collaborations in implementing best practice QA protocols throughout the pharmaceutical supply chain, particularly in the context of global distribution networks.
How does FarmaMondo SA utilize data analytics to identify trends and proactively address potential QA issues before they impact product integrity?
FM and Pharmaceutical companies utilize data analytics in several ways to identify trends and proactively address potential quality assurance (QA) issues before they impact product integrity.
Here's how they and we do it: Monitoring Supply Chain Data, Real-Time Monitoring and Alerting, Root Cause Analysis, Continuous Improvement...
By monitoring key performance indicators (KPIs) such as temperature excursions, humidity levels, transit times, and inventory levels, companies can detect anomalies or deviations from expected norms that may indicate potential QA issues.
Overall, data analytics enables companies to leverage data-driven insights to identify trends, anticipate potential QA issues, and take proactive measures to maintain product integrity throughout the supply chain.
Considering the increasing scrutiny from regulatory bodies, what steps should pharmaceutical companies take to ensure alignment with evolving QA standards while preserving operational flexibility?
To ensure alignment with evolving QA standards while preserving operational flexibility in the face of increasing scrutiny from regulatory bodies, pharmaceutical companies should in my opinion consider the following steps:
Maintain Strong Supplier Relationships: Foster strong partnerships with suppliers, contract manufacturers, and logistics providers to ensure alignment with QA standards throughout the supply chain. Collaborate closely with partners to establish clear quality agreements, conduct regular audits and assessments, and share best practices for maintaining compliance with evolving regulatory requirements.
Strong supplier relationships promote operational flexibility while safeguarding product quality and integrity.
In your opinion, can achieving superior QA become a competitive advantage in the pharmaceutical supply chain? How?
Absolutely! achieving superior Quality Assurance (QA) can indeed become a competitive advantage in the pharmaceutical supply chain.
Here's how: Operational Efficiency and Cost Savings, Customer Satisfaction and Market Differentiation, Continuous Improvement and Innovation...
Customer Satisfaction and Market Differentiation: As Company FM is working on achieving Superior QA in order to contributes to greater customer satisfaction by ensuring product consistency, reliability, and performance. Patients and healthcare professionals value pharmaceutical products with a reputation for quality and efficacy, leading to increased demand, market share, and brand loyalty. We think that Companies that prioritize QA can differentiate themselves in the market, command premium pricing, and gain a competitive advantage over rivals with lower perceived quality standards. In conclusion, achieving superior QA can indeed confer a competitive advantage in the pharmaceutical supply chain by enhancing brand reputation, reducing risk, facilitating market access, improving operational efficiency, enhancing customer satisfaction, and driving innovation.
You are speaking at this year's LogiPharma Asia event. Can you share what the audience can expect to hear from you and what excites you about this event?
Certainly! At LogiPharma Asia this year, attendees can expect to hear insights and strategies on how pharmaceutical companies can leverage technology, innovation, and best practices to optimize their supply chain operations and enhance quality assurance in the rapidly evolving Asian market. I'll be discussing the latest trends, challenges, and opportunities shaping the pharmaceutical supply chain landscape in Asia, with a focus on various topics as: Digital Transformation, Quality Assurance and Regulatory Compliance, Supply Chain Resilience and Agility, Market Access ,Innovation and Collaboration...
What excites me about this event is the opportunity to engage with industry leaders, supply chain professionals, and experts from across the pharmaceutical sector in Asia. It's a chance to share knowledge, exchange ideas, and learn from each other's experiences in navigating the unique challenges and opportunities in this dynamic and rapidly growing region. I look forward to insightful discussions, networking opportunities, and collaborative learning that will inspire attendees to drive positive change and innovation in their organizations' supply chain strategies.
Hear from Dario Bisogni, at Equarius Hotel, Singapore, on 19th June, 11:50 AM for a Keynote Panel Discussion: How can you tailor your supply chain strategy to address regional variations in regulations, infrastructure, and consumer behaviour across the diverse markets you operate in? Find out more here!