Pharma Shortage Fears? Here's How Meds Are Still Getting Delivered
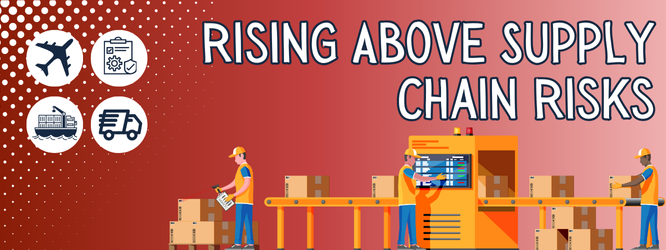
The world of pharmaceuticals is grappling with a stressed supply chain. An unauthorised access to batches of products or emerging drug shortage in the region could cause the delivery of critical medications and patients’ lives to be at stake . The margin for error is razor-thin, and so there is a need to look for existing options to optimise operational efficiency.
To build readiness in face of impending storms ahead, pharma firms need to work alongside logistic providers as their tight collaboration will solidify proactiveness in responding to volatile market conditions and harnessing digital solutions like the control tower to make swift decisions on route optimisation. In this exclusive Q&A interview, Volker Cloos, Director Global Logistics and Supply Chain Asia, Eli Lilly and Company and Brett Marshall, Vice President – Quality & HSSE, Zuellig Pharma unravel their insights on the importance of performing risk mitigation. They stressed on the need to bolster Business Continuity Plan (BCP) procedures, leveraging cost effective benefits for cold chain activities and ensuring their practices and processes show compliance with international standards.
The current situation is not getting any better. Could you share some actions that your company have taken in ensuring the continuity of products for patients?
Volker: As challenges in supply chain and transportation are ongoing and coming from several areas, we must ensure more flexibility as in the past. We are moving more product on air vs. ocean to save some time in transit, but still looking into move back to ocean as much as we see as an opportunity.
Brett: Increased investment in technologies for automation to reduce impact of external factors such as labour resource constraints, while exponentially increasing capacity utilization and operational capabilities of existing facilities and footprints. Also strengthening BCP practices, including expanded training of response teams and increasingly rigorous periodic testing of scenarios across Asia markets.
What more can 3PLs do to support risk mitigation?
Volker: We would expect from 3PL’s especially on cold chain transportation, cost effective solutions. Also, we understand that these transportation challenges add additional complexity, they must look into options and solutions, which can control the increase of logistics cost and also come up with additional controlled cold chain solutions to be able to choose from different options of service and cost.
Brett: They need to be able to respond with agility as situations arise – the agility see during the pandemic has not been maintained and old habits have returned. There needs also to be stronger dialogues on BCP planning and execution, so roles and responsibilities are clearly understood, and readiness is established for when disruption occurs.
Can you share more on how control tower set-up can help in current supply chain situations?
Volker: In the current environment it’s even more important than ever, to have a detailed insight to understand the impact on cost and on the in-transit visibility. This data is key to run a solid bidding process as well.
Brett: Currently, the focus is dealing with multi-sectored transit lanes from manufacturing to in-market partners for onward servicing of hospitals, pharmacies and ultimately patients. There is good progress on “to-market” visibility. This helps significantly for visibility by time and location, and what shipping options are available depending on supply/demand fluctuations, and where disruptions occur which impact route availability and lead-times. Working with partners who have established data capture and transfer capabilities for feeding the control tower is a critical success factor.
How do freight forwarders mitigate theft of cargo?
Volker: I would except that freight forwarder will incorporate TAPA certifications which will help to ensure a high secure but also standardized solution.
Brett: This requires rigorous vetting and management of resources involved in providing service, and for the management of facilities and transit lanes. Qualification of supplier partner helps ensures that 3PL partners have the required practices and processes are in place for secure infrastructure, systems, processes and people. Compliance with international standards, such as TAPA for Facilities Security and Transport Security - TAPA APAC is well organized and highly active in the areas of cargo theft and brand protection, and fighting against counterfeit, substandard and falsified medicines – is highly recommended.
Where do you see RAIL fitting as a reliable mode of transport and mitigation, from Europe to Asia (and vice versa)?
Brett: There have been some trial shipments of pharma product from Europe to China by rail, with reefer containers specifically fitted to ensure temperatures can be maintained for the required periods. Likely though that it will be some time yet before this transit lanes develops to a scale of other modal choices.
Has the need for resilience influenced how you design your supply chains? Have you changed where you hold inventory, or leveraged solutions like Regional DCs?
Volker: This is a very good question. Also, we are looking for bringing more product into the region / RDC’s, we also must understand the impact on the overall inventory impact. Bring product closer to the market is always a good solution, but an enhanced advantage will come as soon as markets are able to share packs or at least only requires a small re-dressing for localization.
Brett: We have also seen partners making strategically significant changes to their supply chain strategies. As an example, one partner now ships vaccines (at 2˚- 8˚C) by sea rather than by sea, shipping to an established RDC in Singapore, where late-stage customization takes place for onward vaccines shipment to meet demand in other Asian markets.
Our Speakers:
Volker Cloos, Director Global Logistics and Supply Chain Asia, Eli Lilly and Company
Brett Marshall, Vice President – Quality & HSSE, Zuellig Pharma